The Minister of Economy, Trade and Industry Prize: Dynax Corporation

The Minister of Economy, Trade and Industry Prize: Dynax Corporation
Source: The Japan Machinery Federation
New Clutch Discs with Durability and Anti-friction Characteristics for Automatic Transmission Vehicles
A clutch disc used in the transmission system (automatic transmission) of automatic (AT) vehicles has an iron ring structure provided with a friction material attached to its surface. In the past, asbestos, which causes serious health problems, was used as a friction material. Dynax Corporation took up the challenge of producing “asbestos-free” materials.
In 1983, they succeeded in developing Japan’s first paper friction material through a process of combining natural and synthetic fibers, blended with a friction adjustment agent, which was impregnated with phenol resin for hardening. This development not only solved an environmental issue but also produced a product that far surpasses conventional materials in terms of various specifications such as durability, thus significantly contributing to the “advancement” of AT vehicles.
With “asbestos-free” as the No.1 priority, challenging the development of friction materials made in Japan
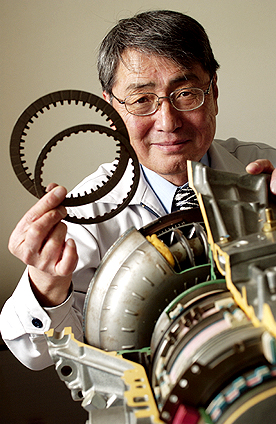
Although now a well-known social issue given the documented damage to health caused by asbestos, the harmful effects of asbestos caused a big controversy in the early 1980s. Currently, 95% of all new models released in Japan are automatic transmission (AT) vehicles. The development of a new type of clutch disc promoted by Dynax played an extremely important role in this situation.
A car equipped with a manual transmission employs one clutch plate that is “manually” manipulated by the driver, whereas gear shifting is done automatically in an AT vehicle through the attachment or separation of a number of clutch discs installed in the transmission system. In order to securely “attach together” the discs when pressed against each other, the disc surfaces are treated with friction materials. Asbestos was previously used for that purpose.
“It was virtually a start from scratch, not an application of some basic development,” remembers Mr. Shibuya, who was presented with the daunting task of developing “asbestos-free materials” immediately after being recruited by the company upon graduating from university in 1981. Naturally, he endured an inevitable period of constant struggle trying to achieve this goal.
“Inside the transmission is filled with lubricating oil, you know. And the discs are pressed against or separated from one another in that condition. I was told to come up with some kind of material that could satisfy the conflicting demand of ‘stop sliding while letting it slide’.”
Although the company had already been developing products involving paper (cellulose) materials, it was decided that providing such materials with the strength necessary to serve as friction materials was impossible. In 1983, they finally reached the starting point of developing domestically produced “paper friction materials” that were still paper-based, but which were to be created according to a different concept and using other materials as well. It took another three or four years to commercialize these materials.
Overcoming the hardship of no sales for four years and reaching the top of the world
Actually, Mr. Shibuya joined the company almost by coincidence. During his job search, he visited the company with a casual feeling of “just popping in here,” but that visit changed the course of his life.
“I had another company in mind, but was overwhelmed by their zealous invitation of ‘start working here from tomorrow’.”
The company was established in 1973. At that time, it had a licensing agreement with an American manufacturer, who imported, processed, and sold products (friction materials). However, being unable to supply products that satisfied the needs of domestic automakers caused the company to endure ‘zero’ sales for four long years after the company was established. Even after that, business results remained sluggish.
A policy was formulated to break through such stagnation, resulting in the in-house development of own products. More specifically, this development manifested itself in the commercialization of “friction materials for clutch discs through asbestos-free production.” This was around that time that Mr. Shibuya dropped by the company. From the company’s perspective, “a university graduate majoring in synthetic chemistry” must have looked like a golden egg that came rolling right in to them.
There are a great variety of friction materials depending on the manufacturer and model of car. Clutch discs for high-output engines are different from others, and transmissions are constantly being downsized. Products providing semi-permanent quality assurance are now the required norm. In order to meet such demanding requirements, you cannot slow down the pace of technological innovation.
“Moving on from paper-based products, we are now promoting the development of non-woven fabric products. We have already reached a commercialization phase where some products will be adopted by certain manufacturers.”
As a result of the high evaluation given to the company, their clutch discs have acquired 40% of the worldwide share for new AT models to be released in 2007. For the first time ever, the company is ranked in the top.
“We entered the market of automotive parts as a latecomer when the ‘affiliated makers’ of the parent automakers dominated the industry, so the only way for us to make a living was to produce the kinds of products that could win their recognition.”
The company’s genetic makeup of challenging spirit plays a big part in supporting today’s automotive industry worldwide.